Wire EDM in Gear Manufacturing and Reverse Engineering at Grupo IAM
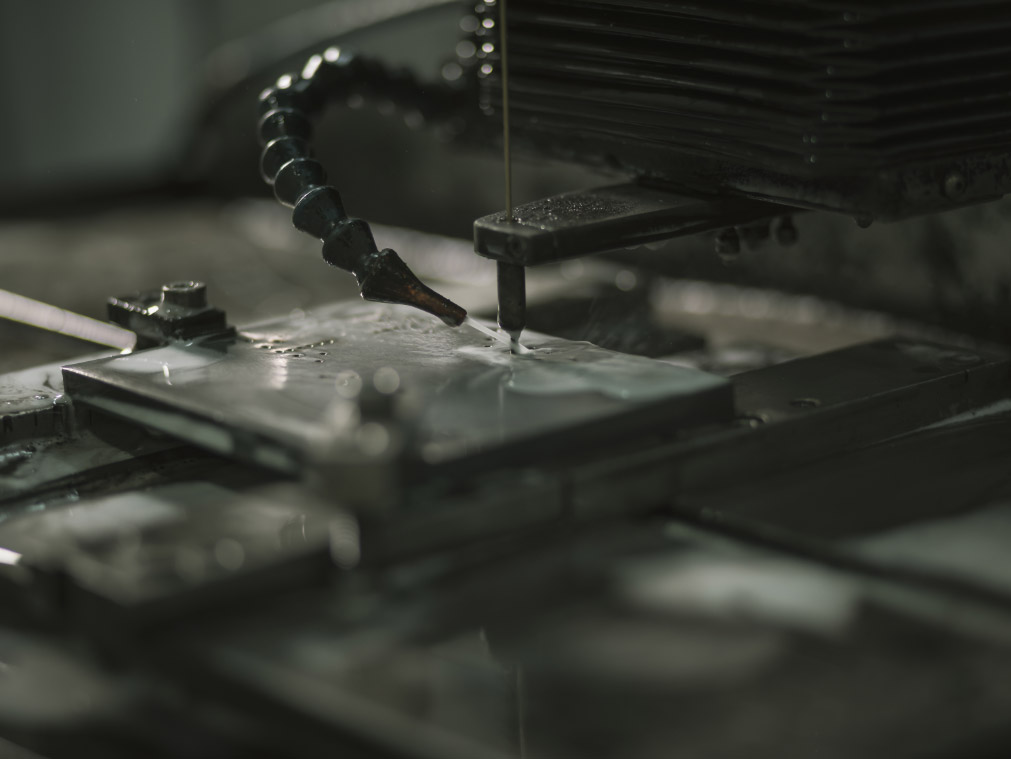
One of the challenges in manufacturing is reverse engineering. Instead of designing a product from scratch, reverse engineering involves starting from an existing object to understand how it was created, what materials were used, how it functions, and how it can be improved or replicated. Reverse engineering can be challenging, especially when blueprints are not available. This was precisely the case faced by Grupo IAM. In the example discussed in this article, wire EDM in gear manufacturing became a crucial process for developing the project.
Wire EDM in Gear Manufacturing Applicable to Various Sectors
The manufacturing process began without a tangible blueprint to guide it. The Grupo IAM team demonstrated its expertise in reverse engineering to overcome this initial challenge. Using wire EDM and FANUC machine technology, it successfully advanced in creating the gears required for the components.
The adopted strategy included using a 3D scanner to measure each tooth of the gear. This process allowed for a detailed blueprint, which was crucial for the next step: creating a control jig. This jig would serve as a verifier during manufacturing and represent valuable know-how for the Grupo IAM team.
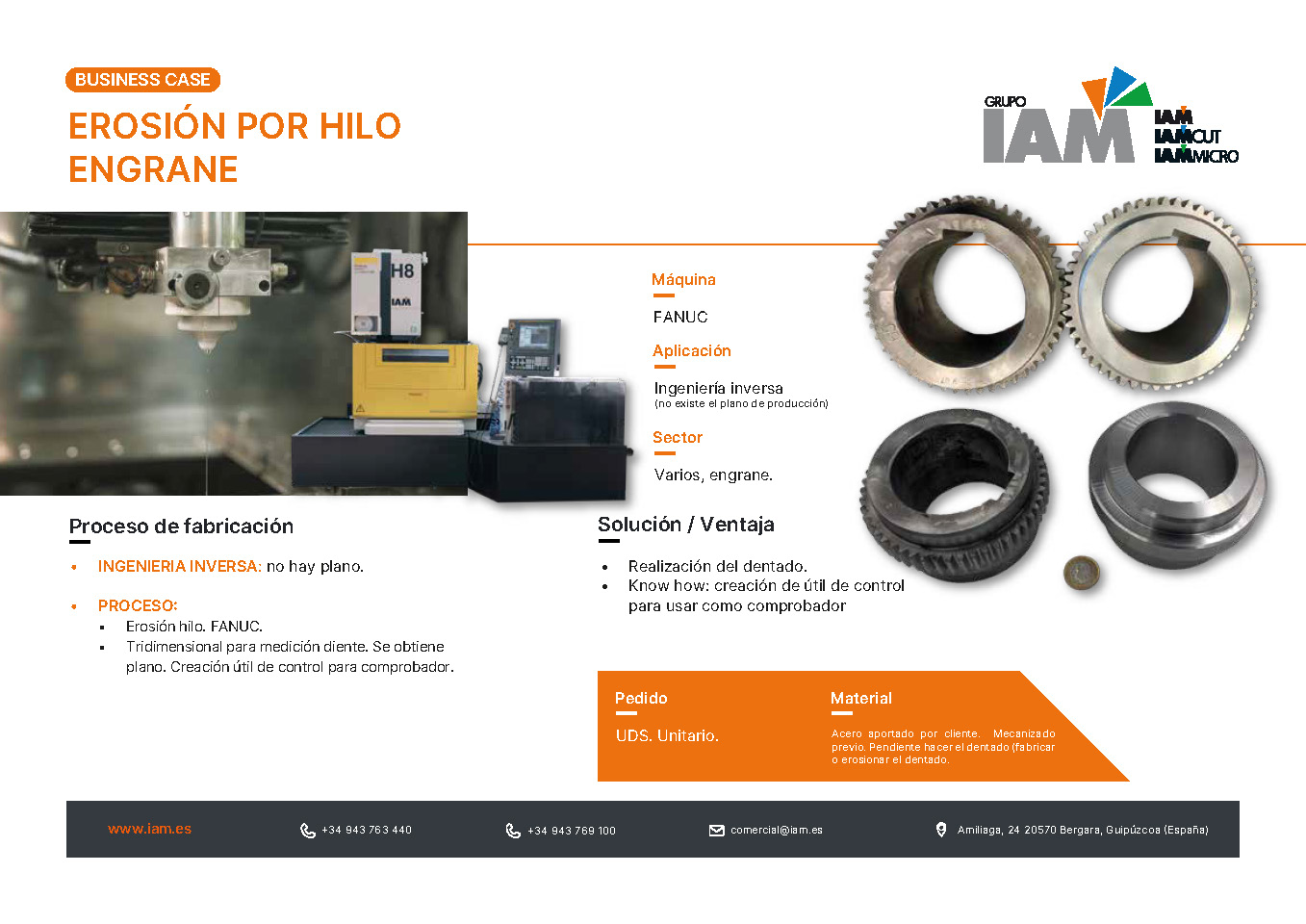
FANUC Wire EDM Machine
The FANUC machine became the essential tool for carrying out this task. Its precision and reliability were crucial for achieving the desired results in the wire EDM process. This project involved gear manufacturing and required careful planning and execution due to the absence of an initial blueprint. The applications for this piece are diverse, as gears are essential components in a wide range of industries.
The client provided the material in steel units. This material required pre-machining before the gear-cutting process could begin, which presented the option of either manufacturing or eroding the teeth.
Grupo IAM, Specialists in Electrical Discharge Machining
Grupo IAM's solution involved effective gear cutting and highlighted their ability to tackle complex challenges through reverse engineering. The creation of the control jig ensured the quality of the final product and added valuable internal knowledge to the company.
Please contact us to learn more about Grupo IAM or the different types of high-precision cutting.