Inconel: Resistance to Corrosion and High Temperatures
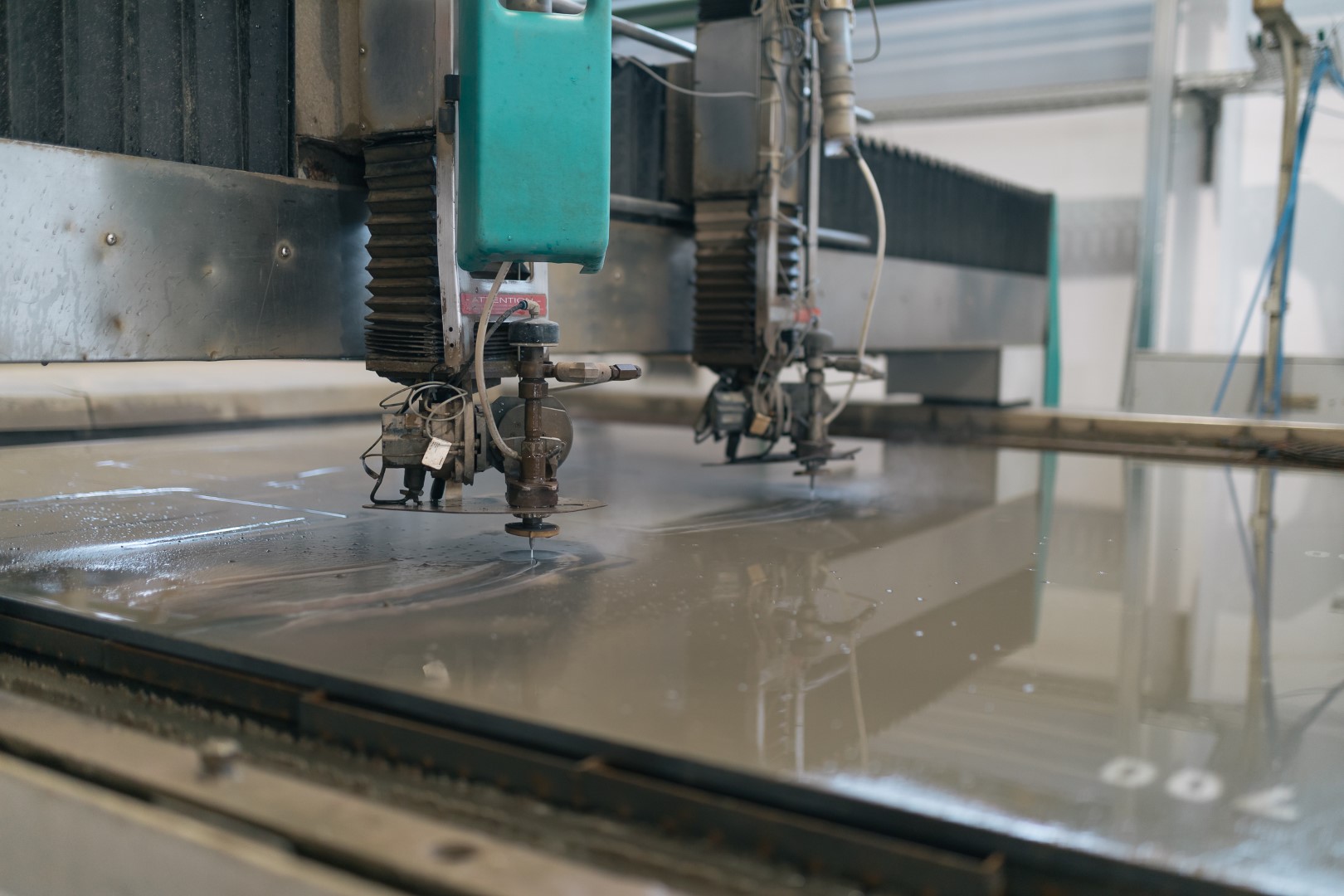
Inconel is a family of nickel-chromium alloys with exceptional properties of resistance to corrosion, oxidation, and high temperatures. First developed by the Special Metals Corporation in the 1940s, Inconel has been widely used in various industrial applications that require superior performance in demanding environments. In this article, we will explore what Inconel is, its distinctive characteristics, standard processing methods, and various applications in the industry.
What is Inconel?
Inconel is a nickel alloy with up to 76% nickel, chromium, iron, and other elements such as molybdenum, titanium, and aluminium. This combination of elements gives Inconel exceptional resistance to corrosion in aggressive environments, including acids, salts, and alkalis, and excellent resistance to oxidation at high temperatures.
Technical Characteristics of Inconel
- Corrosion Resistance: Inconel is highly resistant to corrosion in many environments, making it ideal for applications in the chemical, petroleum, and marine industries, where exposure to corrosive substances is every day.
- High Temperature Resistance: With excellent thermal stability, Inconel maintains its mechanical strength at extremely high temperatures, making it an ideal material for applications in the aerospace, energy, and thermal processing industries.
- Good Fatigue Resistance: Inconel exhibits exceptional resistance to fatigue and stress corrosion cracking, making it suitable for structural components subjected to cyclic loads in hostile environments.
- Ductility: Despite its strength, Inconel retains good elasticity, facilitating its processing and manufacturing into various shapes and configurations.
Inconel can be processed using various techniques, including machining, cold and hot forming, and welding. However, due to its high hardness and strength, machining Inconel can be challenging and requires special cutting tools and appropriate techniques to achieve optimal results.
Cutting Inconel: Electrical Discharge Machining, Water Jet Cutting, and Micro Water Jet Cutting
Cutting Inconel is a standard process in the aerospace and energy industries, requiring precision and resistance to high temperatures and corrosion. Electrical discharge machining (EDM) is a widely used technique for cutting Inconel, involving controlled electrical discharges to erode the material. This method effectively cuts complex shapes and high-hardness materials, although it can be slow and costly.
On the other hand, water jet cutting offers an efficient and versatile alternative for cutting Inconel. This method uses a high-pressure water jet often mixed with abrasives to erode the material. It is fast, generates no heat, and can precisely cut materials of different thicknesses and shapes.
Additionally, micro water jet cutting is a variant of this process that allows exact cuts with minimal heat-affected zones. It is ideal for applications requiring high precision and cut quality under challenging materials like Inconel.
IAM Group: Over 40 Years of High-Precision Cutting
IAM Group can provide its clients high-quality cutting in wire EDM, die-sinking EDM, drilling, water jet cutting, and micro water jet cutting for numerous industrial applications, such as die manufacturing, moulds, and unique parts.
Contact IAM Group; we have the technology, experience, and professionals to meet the current industrial demand in various sectors and all materials.