Micro-cutting by water for automotive engine components
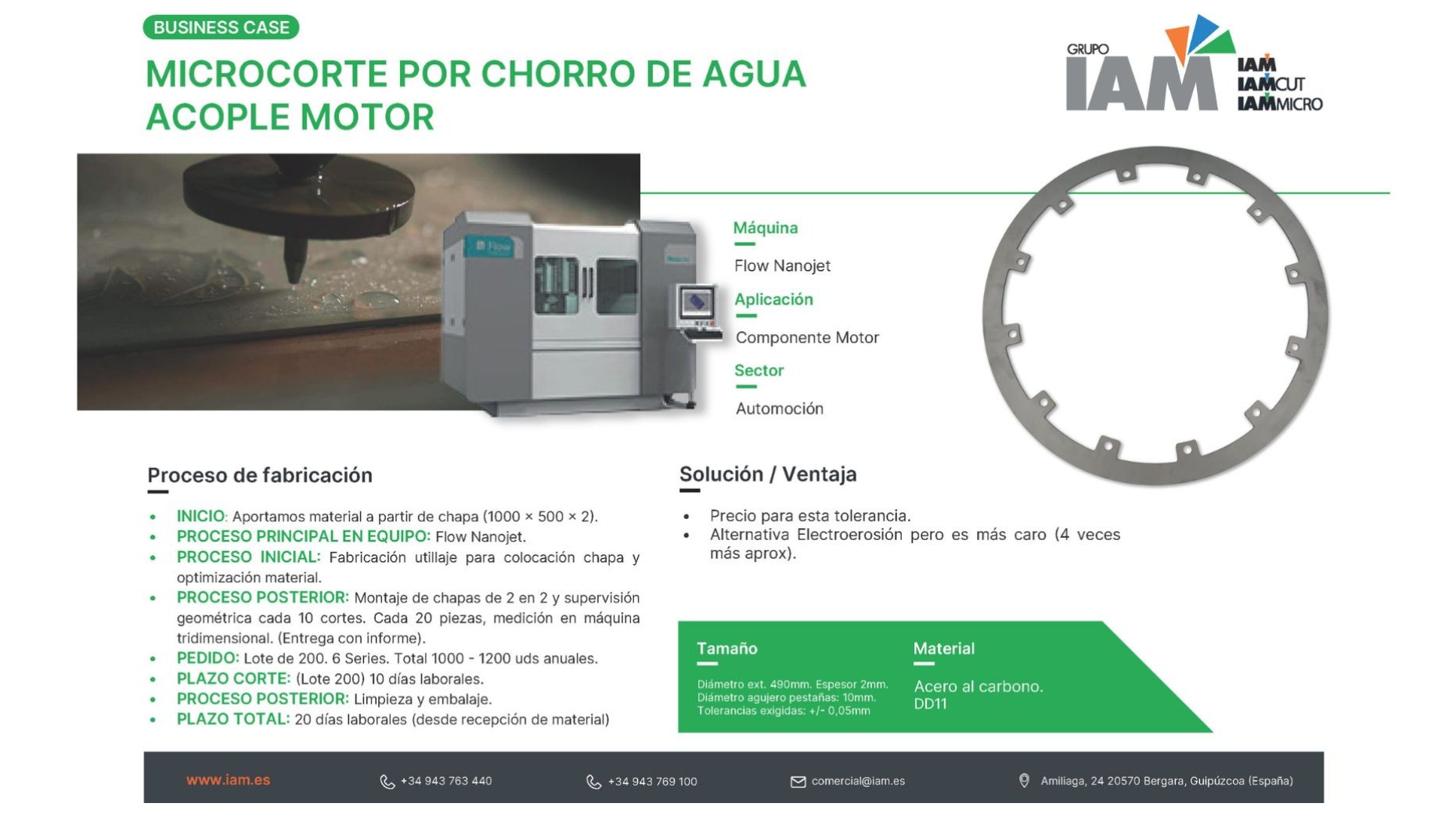
Micro waterjet cutting technology has emerged as an alternative to conventional waterjet cutting. This process offers a high precision and efficiency variation for manufacturing small components while maintaining the virtues of traditional waterjet cutting. The head orifice for the micro-cutting process can be as small as four-tenths of a millimetre in diameter, which also means that the grit size of the abrasive has to be smaller.
Micro waterjet cutting stands out for its ability to work with very tight tolerances, down to +/- 0.03 mm. This capacity makes this type of cutting a process with advantages over conventional waterjet cutting, such as the possibility of generating very complex geometries in all kinds of materials and excellent repeatability and productivity.
Engine coupling: micro waterjet cutting for the automotive sector
One of the highlights of the micro waterjet cutting process is its application in the automotive sector and its production of engine components, among other things. IAM MICRO has optimised this process using its Flow Nanojet machine.
IAM MICRO started the process by supplying material from a carbon steel sheet (1000x500x2), which was then subjected to the precise cutting of the Flow Nanojet machine. The initial sheet was 3000x500, so it was necessary to modify it to the exact size of conventional cutting machines. Subsequently, the parts were extracted and subjected to rigorous geometric and dimensional monitoring.
On this occasion, waterjet micro-cutting was a very suitable option, as the alternative was to use EDM, which would have resulted in a cost of approximately four times higher.
Advantages of micro waterjet cutting
Micro waterjet cutting, in addition to precision and versatility, offers significant advantages for a variety of industries:
High precision ensures uniformity and accuracy of manufactured parts, which is crucial in aerospace, electronics and automotive industries.
Versatility and minimal thermal impact: Unlike some cutting methods that can damage or deform certain materials, waterjet is a non-intrusive technique that can be used on a wide range of materials, including metals, plastics, glass and composites, among others. In addition, micro waterjet cutting does not generate significant heat during the cutting process, thus avoiding thermal deformation of materials.
IAM MICRO, pioneers in waterjet micro-cutting
The IAM Group was the first company in Spain to offer waterjet micro-cutting, which led to the creation of IAM MICRO. From IAM MICRO, we offer precise and efficient solutions for manufacturing small components in various sectors, such as the automotive sector. With a meticulous manufacturing process and a quality-focused approach, IAM MICRO has established itself in the industry, offering its customers high productivity and repeatability for large batches of parts.